はじめに
「金型内アッセンブル成形」(特許出願済み)とは、常識通りにやっていたのでは、これからの時代を生き残れないという認識より生まれた、これまでであれば即座に「不可能」とされていた加工を可能にする常識破りの技術です。
この技術は、モールド型にアクチュエータを組み込み、シーケンサでコントロールし、 部品の成形と組立を金型内部で一貫して行う、同社の放電加工金型の生産技術が基に なっており、「複数部品の成形から組立までを一つの金型の内部でやってしまおう」という技術です。
いわばプレス金型における順送りに似た発想のこの「アッセンブル成形」は、イメージとして言えば、ロータリー射出成形の概念、つまりロータリーテーブルが回転してインサートワークが供給され、次々に必要な成形が行われて、やがて完成品ができあがる、そういった一連の流れをそのまま<1つの金型の中>で実現させる技術です。
これらの独自開発によるユニークな生産技術を、ごく小さい金型構造の中に作り込んで開発されたのが、「アッセンブル成形(金型)」といえます。
アッセンブル成形の実例
「アッセンブル成形(金型)」をよりわかりやすく説明するためにサンプルとして作られたものにギア・アッセンブリー(下図)があります。外径35mmのハウジング内部に複数のギアが構成されたギアレーションです。これを基に写真や図で説明しましょう。
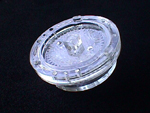
従来はこの7つの部品はそれぞれの7つの金型で成形され、その後に組立てられていたわけですが、「アッセンブル成形(金型)」では1つの金型でこれらの7点の部品の成形・組立を1ショット(1サイクル)で行うことができます。
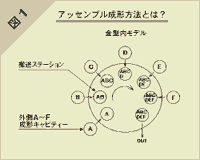
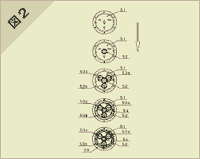
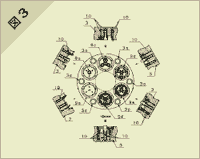
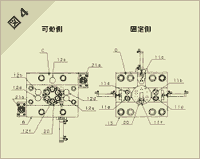
この金型内部の概念を示したのが図1です。外側に成形キャビティがあり、内側には搬送ステーションがあります。キャビティから成形品が搬送ステーションに送り込まれ、その搬送ステーションが回転方向に少しずつずれていくことで順に部品が組みあがっていくことになります。
図2に組立順序の展開図を示します。図3は成形キャビティのレイアウトを、図4は金型への展開図です。外側の成形キャビティで成形された部品は、金型が開いたとき、固定側のキャビティに残り、スライドコアにより、内側の搬送ステーションに移動します。成形品が搬送ステーションに受け渡された後、スライドは外側の成形位置に戻ることになります(図5,6)。
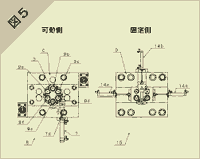
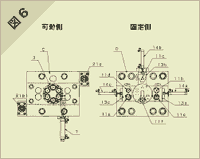
メリット
「アッセンブル成形」のメリットとしては、まず製品設計上のメリットとして「金型から製品ユニットとして出てくるので組立工程が不要であること。次に、従来では不可能だったアンダー形状の加工をすることができること。さらに部品の組立基準・ガイドや加工基準が要らなくなること」が挙げられます。
また、生産技術、生産管理面のメリットとしては「組立工程が削減され、工期が短縮される。必要な個数だけ生産すればよく、部品個々の仕掛品を持つ必要がない。そして組立ユニット間のばらつきがなくなる」ことなども挙げられます。 「アッセンブル成形(金型)」での精度は、形状は、成形品の大きさは、コストダウンの実際はどうか、そして生産技術としての信頼性は・・・など、いま各種テーマに沿った検討が急速に進められていますが、この全く新しい発想の技術を活かす製品開発が待たれるところです。
終わりに
アッセンブル成形はもちろん、様々な複合成形を考えることで、製品設計のあり方を根本的に考え直す必要があると考えられます。単純に従来の組立工程が削除できるという考え方ではなく、この新しい技術にふさわしい、部品設計の自由度の高い、新しい用途分野を拓くものとして位置づけたい。そのためには商品開発、製品設計の段階から金型技術者が形状設計や評価検討に参加する必要性や、こうした生産方式に合わせた新しいタイプのエンジニアの育成などが望まれます。
この技術を受けて、生産機械そのものはどうあるべきなのかという点についても今後考慮を要するテーマです。
アッセンブル成形の製品例は製品情報をご覧下さい。